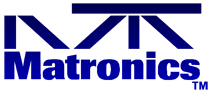 |
Matronics Email Lists Web Forum Interface to the Matronics Email Lists
|
View previous topic :: View next topic |
Author |
Message |
1rv4
Joined: 11 Sep 2006 Posts: 20
|
Posted: Fri Oct 21, 2016 8:32 am Post subject: Coiled ignition systems |
|
|
Hi All
I have finished wiring a very simple single place biplane with a VW engine. The engine has single ignition, automotive style with coil and breaker points. I used a master switch to turn off all power at the contactor which is next to the battery behind the seat. There is also a key ignition switch that is used to start the engine it powers the starter and coil.
So in order to start the plane the master has to be on and then the ignition switch provides power for the starter and ignition. I know this is a two point failure set up, but the alternative is to have the pilot remember to turn off both master and ignition switch in case of emergency, something that probably wouldn't happen in a stressful situation.
Is there a better way to handle coiled ignition systems?
Thanks
Chris
| - The Matronics AeroElectric-List Email Forum - | | Use the List Feature Navigator to browse the many List utilities available such as the Email Subscriptions page, Archive Search & Download, 7-Day Browse, Chat, FAQ, Photoshare, and much more:
http://www.matronics.com/Navigator?AeroElectric-List |
|
|
|
Back to top |
|
 |
user9253
Joined: 28 Mar 2008 Posts: 1908 Location: Riley TWP Michigan
|
Posted: Sat Oct 22, 2016 5:53 am Post subject: Re: Coiled ignition systems |
|
|
If a forced landing is immanent, all electrical power should be shut off to prevent ignition of leaking fuel. A master switch that shuts off everything including the engine is good for that scenario. However, smoke in the cockpit is an emergency that may require shutting off all electrical loads except the engine. In that case, engine ignition needs to be independent of the master switch. The most reliable ignition circuit is less complicated and has fewer components. If it were my plane, I would power the ignition system from the battery, independent of the master switch. The engine starter circuit should be disabled when the master switch is off.
| - The Matronics AeroElectric-List Email Forum - | | Use the List Feature Navigator to browse the many List utilities available such as the Email Subscriptions page, Archive Search & Download, 7-Day Browse, Chat, FAQ, Photoshare, and much more:
http://www.matronics.com/Navigator?AeroElectric-List |
|
_________________ Joe Gores |
|
Back to top |
|
 |
nuckolls.bob(at)aeroelect Guest
|
Posted: Sat Oct 22, 2016 10:03 am Post subject: Coiled ignition systems |
|
|
At 08:53 AM 10/22/2016, you wrote:
Quote: | --> AeroElectric-List message posted by: "user9253" <fransew(at)gmail.com>
If a forced landing is immanent, all electrical power should be shut off to prevent ignition of leaking fuel. A master switch that shuts off everything including the engine is good for that scenario. However, smoke in the cockpit is an emergency that may require shutting off all electrical loads except the engine. In that case, engine ignition needs to be independent of the master switch. The most reliable ignition circuit is less complicated and has fewer components. If it were my plane, I would power the ignition system from the battery, independent of the master switch. The engine starter circuit should be disabled when the master switch is off. |
Agreed . . .
Since your ignition system will run nicely
on 7A or less, I too would recommend you
run the ignition directly from the battery
through a 7A fuse. Power the starter from
the bus powered through the master contactor.
The ignition circuit is low risk for post-crash
ignition source . . . so even if you don't
get the engine killed before anticipated
contact the primary risk is to the engine
having a powered prop strike.
Taking everything else through the battery
master is the conventional philosophy.
Bob . . .
| - The Matronics AeroElectric-List Email Forum - | | Use the List Feature Navigator to browse the many List utilities available such as the Email Subscriptions page, Archive Search & Download, 7-Day Browse, Chat, FAQ, Photoshare, and much more:
http://www.matronics.com/Navigator?AeroElectric-List |
|
|
|
Back to top |
|
 |
yellowduckduo(at)gmail.co Guest
|
Posted: Sat Oct 22, 2016 11:39 am Post subject: Coiled ignition systems |
|
|
A 7 amp CB seems reasonable but a 7 amp fuse makes me a bit nervous. I
seem to recall that when I looked at ignition currents I noted that they
went up at high rpm, at high temperatures, and in some rare cases when
the engine was not turning. I did not notice any automotive systems
that lightly fused the ignition circuits. So while I've never measured
over 5 amps on my soob units, my personal recommendation is a minimum 10
amp fuse on ignition circuits that feed multiple cylinders even if they
are solid state. It may be that the peak currents as seen on a scope
caught my attention or that I just like more headroom on critical fuses.
I think part of my thought process might have been that on my system if
one solid state coil driver shorted full on it would not necessarily
take out the system fuse. I don't have any idea what the tolerance is on
an ATC fuse. I have 700 hours on the original 10 amp fuses that feed the
4 cylinder soob. I've had two cases of one cylinder losing power due to
a partial coil failure. Once during initial ground testing and once at
around 500 hours. These are DIS coils that each feed two cylinders but
in both cases only one cylinder lost power.
Ken
On 22/10/2016 2:02 PM, Robert L. Nuckolls, III wrote:
Quote: | At 08:53 AM 10/22/2016, you wrote:
>
>
> If a forced landing is immanent, all electrical power should be shut
> off to prevent ignition of leaking fuel. A master switch that shuts
> off everything including the engine is good for that scenario.
> However, smoke in the cockpit is an emergency that may require
> shutting off all electrical loads except the engine. In that case,
> engine ignition needs to be independent of the master switch. The
> most reliable ignition circuit is less complicated and has fewer
> components. If it were my plane, I would power the ignition system
> from the battery, independent of the master switch. The engine
> starter circuit should be disabled when the master switch is off.
Agreed . . .
Since your ignition system will run nicely
on 7A or less, I too would recommend you
run the ignition directly from the battery
through a 7A fuse. Power the starter from
the bus powered through the master contactor.
The ignition circuit is low risk for post-crash
ignition source . . . so even if you don't
get the engine killed before anticipated
contact the primary risk is to the engine
having a powered prop strike.
Taking everything else through the battery
master is the conventional philosophy.
Bob . . .
|
| - The Matronics AeroElectric-List Email Forum - | | Use the List Feature Navigator to browse the many List utilities available such as the Email Subscriptions page, Archive Search & Download, 7-Day Browse, Chat, FAQ, Photoshare, and much more:
http://www.matronics.com/Navigator?AeroElectric-List |
|
|
|
Back to top |
|
 |
ceengland7(at)gmail.com Guest
|
Posted: Sat Oct 22, 2016 12:54 pm Post subject: Coiled ignition systems |
|
|
Ken brings up an easy redundancy opportunity. Some (most?) automotive
style engine controllers switch the ground side of the coils and the
injectors. To limit the impact of such failures, I chose to
independently fuse each coil. Might be worth a look if running an auto
style engine controller.
Charlie
On 10/22/2016 2:37 PM, C&K wrote:
Quote: |
A 7 amp CB seems reasonable but a 7 amp fuse makes me a bit nervous. I
seem to recall that when I looked at ignition currents I noted that
they went up at high rpm, at high temperatures, and in some rare cases
when the engine was not turning. I did not notice any automotive
systems that lightly fused the ignition circuits. So while I've never
measured over 5 amps on my soob units, my personal recommendation is a
minimum 10 amp fuse on ignition circuits that feed multiple cylinders
even if they are solid state. It may be that the peak currents as
seen on a scope caught my attention or that I just like more headroom
on critical fuses. I think part of my thought process might have been
that on my system if one solid state coil driver shorted full on it
would not necessarily take out the system fuse. I don't have any idea
what the tolerance is on an ATC fuse. I have 700 hours on the original
10 amp fuses that feed the 4 cylinder soob. I've had two cases of one
cylinder losing power due to a partial coil failure. Once during
initial ground testing and once at around 500 hours. These are DIS
coils that each feed two cylinders but in both cases only one cylinder
lost power.
Ken
On 22/10/2016 2:02 PM, Robert L. Nuckolls, III wrote:
> At 08:53 AM 10/22/2016, you wrote:
>>
>>
>> If a forced landing is immanent, all electrical power should be shut
>> off to prevent ignition of leaking fuel. A master switch that shuts
>> off everything including the engine is good for that scenario.
>> However, smoke in the cockpit is an emergency that may require
>> shutting off all electrical loads except the engine. In that case,
>> engine ignition needs to be independent of the master switch. The
>> most reliable ignition circuit is less complicated and has fewer
>> components. If it were my plane, I would power the ignition system
>> from the battery, independent of the master switch. The engine
>> starter circuit should be disabled when the master switch is off.
>
> Agreed . . .
>
> Since your ignition system will run nicely
> on 7A or less, I too would recommend you
> run the ignition directly from the battery
> through a 7A fuse. Power the starter from
> the bus powered through the master contactor.
>
> The ignition circuit is low risk for post-crash
> ignition source . . . so even if you don't
> get the engine killed before anticipated
> contact the primary risk is to the engine
> having a powered prop strike.
>
> Taking everything else through the battery
> master is the conventional philosophy.
>
>
> Bob . . .
>
|
| - The Matronics AeroElectric-List Email Forum - | | Use the List Feature Navigator to browse the many List utilities available such as the Email Subscriptions page, Archive Search & Download, 7-Day Browse, Chat, FAQ, Photoshare, and much more:
http://www.matronics.com/Navigator?AeroElectric-List |
|
|
|
Back to top |
|
 |
nuckolls.bob(at)aeroelect Guest
|
Posted: Sun Oct 23, 2016 4:51 am Post subject: Coiled ignition systems |
|
|
At 02:37 PM 10/22/2016, you wrote:
Quote: | --> AeroElectric-List message posted by: C&K <yellowduckduo(at)gmail.com>
A 7 amp CB seems reasonable but a 7 amp fuse makes me a bit nervous. I seem to recall that when I looked at ignition currents I noted that they went up at high rpm, at high temperatures, and in some rare cases when the engine was not turning. |
The Kettering-coil style ignition system
draws the most with engine stopped and points
closed. Current goes down after engine starts
and slightly less at higher rpm.
Quote: | I did not notice any automotive systems that lightly fused the ignition circuits. |
No rational for doing it in cars . . . all fused
feeders are relatively robust with respect to
their loads. In the case of an always-hot
battery feed, the AVIATION rational is 5A
max breakered, 7A max fused. For a Kettering
coil/points system, 7A fusing is very robust.
Quote: | So while I've never measured over 5 amps on my soob units, my personal recommendation is a minimum 10 amp fuse on ignition circuits that feed multiple cylinders even if they are solid state. |
Those are CDI or other more modern techology
and DO behave differently from the Kettering
coil/points system.
Quote: | It may be that the peak currents as seen on a scope caught my attention or that I just like more headroom on critical fuses. I think part of my thought process might have been that on my system if one solid state coil driver shorted full on it would not necessarily take out the system fuse. I don't have any idea what the tolerance is on an ATC fuse. I have 700 hours on the original 10 amp fuses that feed the 4 cylinder soob. I've had two cases of one cylinder losing power due to a partial coil failure. Once during initial ground testing and once at around 500 hours. These are DIS coils that each feed two cylinders but in both cases only one cylinder lost power. |
Understand . . . but that's a different
breed of cat . . .
Even so, even real beastly electronic CDI
systems (Lightspeed comes to mind) only
draw 2.5A at 28V into a constant-power
switchmode power supply . . . so 5A at 14V
for a 6 cylinder engine at red-line rpm.
That's a LOT of watts. Waaayyyy more than
necessary but I think Klaus's engines are expected to
run on spark-power alone (just kidding).
But consider a 10A feeder in an automobile:
7A continuous is a reasonable load factor for
a 10A fuse. In a 14v system 7A is 100 watts.
There's just no reason that the ignition
system should use such power. Consider the
ignition excitation system on a Rotax that
a gets fly-by of a single magnet once every
crankshaft revolution . . . compare that with
the array of magnets, windings and cores on
the same flywheel designed to 18A at 14 volts
or 250 watts . . . a huge difference in energy
budgets/requirements.
But your point is well taken and the caveat
here is to KNOW the requirements your particular
system. When in doubt measure it.
Bob . . .
| - The Matronics AeroElectric-List Email Forum - | | Use the List Feature Navigator to browse the many List utilities available such as the Email Subscriptions page, Archive Search & Download, 7-Day Browse, Chat, FAQ, Photoshare, and much more:
http://www.matronics.com/Navigator?AeroElectric-List |
|
|
|
Back to top |
|
 |
user9253
Joined: 28 Mar 2008 Posts: 1908 Location: Riley TWP Michigan
|
Posted: Sun Oct 23, 2016 6:22 am Post subject: Re: Coiled ignition systems |
|
|
This discussion reminds me of the electric fire pump motor at work. I can not remember the size, but it was a big motor, 50 or 100 HP, 3 phase, 480 volts. There was no circuit protection, just a disconnect switch. The reasoning is that it is more important to save the factory from fire than to protect the fire pump motor or wiring. If anyone is interested, you can read about fire pump requirements:
http://ecmweb.com/code-basics/power-pump
Some aircraft builders might apply the same reasoning to their engine ignition system by using an oversize fuse. They would rather have the wires and coils burn up than take a chance on a fuse blowing and the engine quitting. Of course smoking components should be on the engine side of the firewall.
I am not recommending a fuse size that would actually allow wires to smoke, just saying that a fuse could be one or two sizes bigger for a critical application.
| - The Matronics AeroElectric-List Email Forum - | | Use the List Feature Navigator to browse the many List utilities available such as the Email Subscriptions page, Archive Search & Download, 7-Day Browse, Chat, FAQ, Photoshare, and much more:
http://www.matronics.com/Navigator?AeroElectric-List |
|
_________________ Joe Gores |
|
Back to top |
|
 |
rnjcurtis(at)charter.net Guest
|
Posted: Sun Oct 23, 2016 7:39 am Post subject: Coiled ignition systems |
|
|
This discussion reminds me of the electric fire pump motor at work. I can not remember the size, but it was a big motor, 50 or 100 HP, 3 phase, 480 volts. There was no circuit protection, just a disconnect switch. The reasoning is that it is more important to save the factory from fire than to protect the fire pump motor or wiring. If anyone is interested, you can read about fire pump requirements:
http://ecmweb.com/code-basics/power-pump
Some aircraft builders might apply the same reasoning to their engine ignition system by using an oversize fuse. They would rather have the wires and coils burn up than take a chance on a fuse blowing and the engine quitting. Of course smoking components should be on the engine side of the firewall.
I am not recommending a fuse size that would actually allow wires to smoke, just saying that a fuse could be one or two sizes bigger for a critical application.
I would (ass u me) that the manufacturer’s specs on installation of an electronic ignition would spec wires to handle the maximum current draw of the unit under all operating conditions. If one were to fuse it to these specs, then there should be no wire burning, and the fuse will not blow unless there is a failure causing more than the maximum current flow. This might mean that if you have a “current hungry” device, the fuse could possibly be a bit larger than the 7 amp max normally specified on production aircraft. If you have a problem with using a larger fuse, even though it is protecting your wiring, then I would suggest that the alternative is to purchase and install an ignition system with a current draw that is within your comfort zone.
Roger
| - The Matronics AeroElectric-List Email Forum - | | Use the List Feature Navigator to browse the many List utilities available such as the Email Subscriptions page, Archive Search & Download, 7-Day Browse, Chat, FAQ, Photoshare, and much more:
http://www.matronics.com/Navigator?AeroElectric-List |
|
|
|
Back to top |
|
 |
nuckolls.bob(at)aeroelect Guest
|
Posted: Mon Oct 24, 2016 9:24 am Post subject: Coiled ignition systems |
|
|
I would (ass u me) that the manufacturer's specs on installation of an electronic ignition would spec wires to handle the maximum current draw of the unit under all operating conditions.
Actually, the manufacture should be silent on
the matter of wire sizes and protection OUTSIDE
their product's boundaries.
The classic interface specification for aircraft
hardware speaks to a 'box' . . . some kind of device
or collection of devices with goesintas and goesoutas.
I.e. you supply operating energy and control command
inputs to effect the specified result whether that's sparks,
noises from the headphones, or fluid flows to the engine
as outputs.
You also list limits for which the product is designed
and tested to tolerate which included but are not
limited to performance, extraordinary demands, environment,
etc.
This philosophy offers a set of conditions that are
easily verified during qualification and manufacturing
in the laboratory environment. This is how we get the
'good housekeeping seal of approval' on the various
mechno and electro-whizzies totally independent of
the products ultimate application.
It is up to the system designer to evaluate capabilities
and limits for the sub-system for suitability to task
in the super-system. This would include a failure mode
effects analysis and characterizing the risks to
aluminum and body parts should expectations not
be realized.
The fire-fighting pump narrative is interesting . . .
it was probably the sum total of regulatory effects
for two or more committees . . . who don't talk
to each other . . . never had to fight a fire . . .
and don't do system integration tasks aided by
thoughtful FMEA.
In the case of our single Kettering ignition system,
exactly what kind of fault might we suppose would
demand an extra-ordinary amount of energy yet
have no effect on normal or even crippled
operation of the ignition system?
Get out your hammers, picks, soldering irons . . .
any tool of your choice and create a fault within
the system that falls within the scenario of
concern.
In the case of single, battery-powered Kettering
(or even more modern automotive) ignition systems,
we're evaluating the same risks tackled by
all auto-conversion configurations since
the DH Pietenpol bolted the model A engine
into the Air Camper.
http://tinyurl.com/jxctbso
http://tinyurl.com/z5syrtf
Interestingly enough, the model T engine was
wwaayyyy ahead of its time. Like modern automobiles,
each spark plug enjoyed its own, dedicated ignition
coil. This offered some level of failure tolerance
for the coils each of which behaved much like the
'shower of sparks' system and featured its
own set of vibrator points and 'condenser'.
[img]cid:.0[/img]
The fundamentals for storing energy on an
inductor, using 'transformer action' of a
high ratio secondary, periodic charging
and release of the energy through a switch
and value of adding a capacitor across that
switch to improve spark performance and
switch life were well understood. The Ford
system described above illustrates application
of those principals.
Tesla knew these things too as illustrated
in his patent of 1893.
http://tinyurl.com/gro5ruq
But Kettering took those simple ideas and
distilled them down to the simplest, most
robust configuration that was also manufacture
friendly. Not that in the Kettering patent,
the system steil featured the 'buzzer', 'vibrator'
or 'tembler' to provide multiple sparks per timing
intervale.
Later all the car manufactures capitalized on A.
Kent's improved ignition coil ideas such that
multiple sparking was no longer necessary. The
vibrator went away (but was still use to boost
magneto cranking performance aka "shower of sparks").
Yes, engine operation is real important for
staying airborne. Assuming one chooses
to fly with a single, battery powered ignition
system, what value is secured by making the
power feeder to that system extra robust with
respect to current draw?
Further, what's the demonstrated history of
the Kettering style system. I've driven hundreds
of thousands of miles behind such systems with
nary a single engine-crippling failure of the
ignition system.
The factor germane this thread becomes clear
with understanding how the various systems
work . . . after knowing everything there is
to know . . . exactly what condition MIGHT
arise in the field to produce a system that
draws too much current but still functioning?
This question is tsame whether you're contemplating
a Model A engine with a stock Ford ignition in a
Pietenpol or a I0-540 with Light Speed's spark
plug blaster
Recall that the overwhelming majority of engine
failures in airplanes are the result of fuel
exhaustion. Mechanical failures come next.
Given our understanding and experience with
the Kettering system, what are the real risks
loss of the ignition due to component wear-out
or gross failure?
It would be interesting to talk to the Corvair
jockies. But I'd beet a case of beer to a pack
of chewing gum that any ignition failures they
have experienced were borne of poor maintenance
or craftsmanship as opposed to unexpected
component failure.
Bottom line is that there is little 'comfort'
to be secured with fatter fuses and wires . . .
and much comfort to knowing the system's
performance and limits and then doing the FMEA
drives risks to acceptably low levels. I suggest
further that the fire water pump analogy is
not particularly meaningful in the well crafted
heavier than air flying machine.
Bob . . .
| - The Matronics AeroElectric-List Email Forum - | | Use the List Feature Navigator to browse the many List utilities available such as the Email Subscriptions page, Archive Search & Download, 7-Day Browse, Chat, FAQ, Photoshare, and much more:
http://www.matronics.com/Navigator?AeroElectric-List |
|
Description: |
|
Filesize: |
113.24 KB |
Viewed: |
11115 Time(s) |
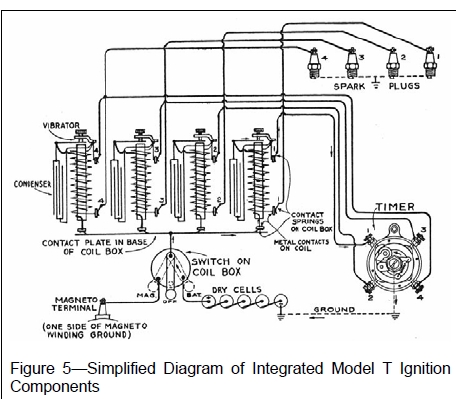
|
|
|
Back to top |
|
 |
lm4(at)juno.com Guest
|
Posted: Mon Oct 24, 2016 12:03 pm Post subject: Coiled ignition systems |
|
|
On Oct 24, 2016, at 1:22 PM, Robert L. Nuckolls, III wrote:
Quote: | I suspect the fire fighting pump story could br referenced to
that part of the NEC wheras one is forbidden to fuse or
breaker conductors when the failure of the equipment will
put lives at risk.
| Larry
Quote: | The fire-fighting pump narrative is interesting . . .
it was probably the sum total of regulatory effects
for two or more committees . . . who don't talk
to each other . . . never had to fight a fire . . .
and don't do system integration tasks aided by
thoughtful FMEA.
|
____________________________________________________________
1 Trick To Erase Eye Bags & Wrinkles In 1 Minute
Daily Tiply
http://thirdpartyoffers.juno.com/TGL3142/580e68bc35b268bb06f2st03duc

| - The Matronics AeroElectric-List Email Forum - | | Use the List Feature Navigator to browse the many List utilities available such as the Email Subscriptions page, Archive Search & Download, 7-Day Browse, Chat, FAQ, Photoshare, and much more:
http://www.matronics.com/Navigator?AeroElectric-List |
|
|
|
Back to top |
|
 |
nuckolls.bob(at)aeroelect Guest
|
Posted: Mon Oct 24, 2016 4:04 pm Post subject: Coiled ignition systems |
|
|
At 03:02 PM 10/24/2016, you wrote:
Quote: | On Oct 24, 2016, at 1:22 PM, Robert L. Nuckolls, III wrote:
Quote: | I suspect the fire fighting pump story could br referenced to
that part of the NEC wheras one is forbidden to fuse or
breaker conductors when the failure of the equipment will
put lives at risk. |
|
Does it really read that way? the whole idea
behind conductor protection is to (1) prevent
catastrophic failure of the conductor with
the attendant risk of smoke, fire and propagation
of the failure event to other conductors and
their systems. And (2) prevent
a failure from propagating upstream . . . the
i(squared)*t constant for the upstream protection
must be some large factor greater than any
single protection . . . lest a short in your
toaster turn out the neighborhood lights.
I've demonstrated that a 22AWG wire, normally
loaded to less than 5A, is not at serious
risk for failure at loads up to 20A.
http://tinyurl.com/h3zlpta
Current limiters in airplanes (while they
have the general appearance of fuses) have
very robust I^2*T numbers. they protect
wires from hard faults while avoiding nuisance
trips due to opening transients due to
operation of a downstream protector.
There are fuses and breakers, then there
are FUSES and BREAKERS. I suggest there are
NO situations where feeders for any device
cannot be selected to meet design/risk goals
without making vague blanket statements about
'putting lives at risk'.
Circuit protection has always been about avoinding
risk to folks and hardware . . . it's just a matter
of picking the right protection.
Bob . . .
| - The Matronics AeroElectric-List Email Forum - | | Use the List Feature Navigator to browse the many List utilities available such as the Email Subscriptions page, Archive Search & Download, 7-Day Browse, Chat, FAQ, Photoshare, and much more:
http://www.matronics.com/Navigator?AeroElectric-List |
|
|
|
Back to top |
|
 |
user9253
Joined: 28 Mar 2008 Posts: 1908 Location: Riley TWP Michigan
|
Posted: Mon Oct 24, 2016 4:30 pm Post subject: Re: Coiled ignition systems |
|
|
Quote: | Overcurrent protection [695.6(D)]. Overcurrent protection devices (OCPDs) must be sized to carry the sum of the locked-rotor current of the fire pump and pressure maintenance pump motor(s) indefinitely, and 100% of the ampere rating of the fire pump's accessory equipment. |
In other words, there is no over current protection, but there is short circuit protection.
| - The Matronics AeroElectric-List Email Forum - | | Use the List Feature Navigator to browse the many List utilities available such as the Email Subscriptions page, Archive Search & Download, 7-Day Browse, Chat, FAQ, Photoshare, and much more:
http://www.matronics.com/Navigator?AeroElectric-List |
|
_________________ Joe Gores |
|
Back to top |
|
 |
lm4(at)juno.com Guest
|
Posted: Mon Oct 24, 2016 4:40 pm Post subject: Coiled ignition systems |
|
|
On Oct 24, 2016, at 8:03 PM, Robert L. Nuckolls, III wrote:
Quote: | At 03:02 PM 10/24/2016, you wrote:
|
Quote: | It doesn't read exactly that way and I have forgotten how exactly how it does read.
But, I do remember that there was a main breaker, fused, for much more than the wire
|
would need for protection. The conductors were kept in their own conduit and the
overload protection on the motor of the gantry crane had to be removed.
That sounds a lot like the fire protection motor. At least it does to me
| - The Matronics AeroElectric-List Email Forum - | | Use the List Feature Navigator to browse the many List utilities available such as the Email Subscriptions page, Archive Search & Download, 7-Day Browse, Chat, FAQ, Photoshare, and much more:
http://www.matronics.com/Navigator?AeroElectric-List |
|
|
|
Back to top |
|
 |
|
|
You cannot post new topics in this forum You cannot reply to topics in this forum You cannot edit your posts in this forum You cannot delete your posts in this forum You cannot vote in polls in this forum You cannot attach files in this forum You can download files in this forum
|
Powered by phpBB © 2001, 2005 phpBB Group
|